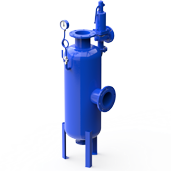
Detail
Vira Flash Steam Tank
Vira vertical flash steam tank is mounted to the condensate return, allowing the flash steam to be released in the condensate at high pressure and temperature. This flash steam is transferred to use a lower pressure process and to increase energy efficiency.
What is Flash Steam?
Flash steam is the name given to low pressure steam that occurs when a high pressure condensate is released into a lower pressure environment in a steam system.
Flash steam can sometimes be seen as a very low value waste product compared to steam produced directly in the boiler. This thought can be a rather expensive mistake. Failure to use flash steam may cause serious energy loss and inefficiency in the system.
Flash steam is a highly efficient heat carrier. When it is not considered as waste, it significantly increases both system efficiency and energy efficiency.
In addition, if the flash steam is not controlled, it is very dangerous both for human health and for the structure it is in.
Flash steam is a good heat carrier rather than being waste.
Steam tables show that when the steam condenses, approximately 25% of its heat turns into condensate. While the correct flash steam recovery system varies according to system temperatures and pressures, approximately half of this heat can be recovered as flash steam.
With the correctly designed flash steam recovery system, the flash steam is released into a tank instead of the atmosphere. The low pressure steam obtained here can be integrated and reused in low pressure applications such as site heating.
To establish an effective flash steam recovery system, it must have 3 basic features.
1- There must be enough high pressure condensate to release enough flash steam. By this way, flash steam recovery will become economical.
2- The recycled flash must have a low pressure application area for steam.
3- Flash steam application should be reasonably close to the high pressure condensate source. Otherwise, the pipe diameters to be used will be high and these systems will be expensive to install in the long term.
Flash Steam Amount Calculation
Let's consider a process that uses steam at 8 bar pressure. The enthalpy of the steam at this pressure is 2775.8 kj / kg steam, which gives the heat of evaporation at the end of heating, turns into condensate with the same pressure and contains 743.6 kj / kg enthalpy.
Suppose that after the steam trap, the condensate empties into a tank at a pressure of 1 bar. In the steam table, the enthalpy of water at 1 bar pressure is 505,8 kj / kg. As seen, according to the saturation state; An excess of 237,8 kj / kg of energy is released and this energy evaporates some of the condensate. This steam is called flash steam.
We can use the formula below to calculate the amount of Flash Steam generated.
Flash Steam Amount: (Hf1-Hf2) / Hfg2
Hf1: Enthalpy of condensate at high pressure (enthalpy of condensate at 8 bar = 743.6 kj / kg)
Hf2: Low pressure condensate enthalpy (enthalpy of condensate at 1 bar = 505,8 kj / kg)
Hfg2: Evaporation enthalpy of steam at low pressure (evaporation enthalpy of steam at 1 bar 2202.3 kj / kg)
Flash vapor Ratio = 0.10 = 10%
Note: You can get support for the saturated steam table from https://en.viraisi.com/saturated-steam-table
Let us assume that the condensate load in this process is 1200 kg / h.
1200 kg / h * 10% = 120 kg / h (Flash Steam Amount)
1200 - 120 = 1080 kg / h (Condensate Amount)
Flash steam tank can be selected according to these data.
Issues to be considered while designing the flash steam tank;
1- Tank diameter should be chosen in a way to ensure that steam flows to the upper outlet at a speed of 3 times.
2- The inlet of the condensate should be taken from the bottom at 1/3 of the tank length.
3- The diameter of the flash steam tank should be the diameter that will allow the condensate to pass before turbulence occurs.
4- Both the inlet and flash steam outlet diameters should be chosen so as not to exceed 15 m / s speed.
Body | : | Carbon Steel |
Connection | : | Flanged |
Max. Working Pressure | : | 14 bar |
Max. Working Temperature | : | 198 °C |
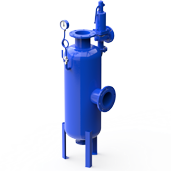